Table of Contents
ToggleNow that we’ve improved the two fundamentals of multi-spindle production, being able to place the part repeatedly in the same position at every index, and being able to deliver the cutting edge to the same point every time, we can leverage some of this machine’s unique CNC abilities to deliver more accurate parts. The HYBRID has the ability to offset each of these tools, for every spindle independently, in .0001” increments. That’s a huge deal for anyone running parts on a Davenport now. You can’t pick a tenth off using mechanical turnbuckles on a machine. Now you have the ability to run your first 5 parts, and DIGITALLY dial in the nominal size spindle by spindle for each tool. You can hold a very narrow tolerance band across all five spindles on your machine, and all without mechanical adjustment.
As your tools wear, you have a “One Touch” adjustment for each tool, so as your average part size starts to grow a few tenths from nominal, you can go into the control, on the fly, and digitally adjust your form tool to bring those parts back into the middle of your part tolerance.
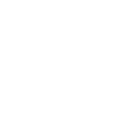
Hybrid Design Machine Features Infographic
Next Gen Controls
The HYBRID has been upgraded with a new, state of the art, CNC control package. It boasts a 15-inch, color touchscreen display, engineered for rugged machine shop environment. The large screen size allowed us to combine multiple small pages of the older controls into a much more user-friendly layout. Fewer pages means less switching between screens and fewer menu layers to get to the functions you need most. Color-coded information is easier to absorb than text, and allows us to direct the operators attention to the most vital information quickly. Everyone owns a smartphone or I-pad, and everything is touchscreen. That’s how people think and expect to interact with their technology.
Energy Efficiency
This technology is not just a pretty face. The hardware hidden inside the control cabinet is designed for maximum reliability and energy efficiency. With drive features like power-on-demand and regenerative braking, the HYBRID uses 50% less electricity, and generates 50% less waste heat than previous Davenport platforms. You save money twice, lowering your machine electricity consumption, and your Air Conditioning bills at the same time.
Size Control
In an experiment on size control, we took one of our customer’s machine run-off tests and applied it across all three of our platforms, with the exact same tooling, speeds, and feeds on all three machine models.
The Model-B machine’s part size distribution tends to be very broad, with lot of outliers, big and small parts. As you step up to the HP, you tend to see a tighter distribution. The HP can make parts that are 2 to 3 times better than the Model-B. But the star of the show is the HYBRID, which was able to put all of its parts within a 4 or 5 tenth band.
This speaks volumes about what the HYBRID platform can do.
Operator Training
For some, CNC technology can be intimidating. That’s why we involved both experienced CNC users, and traditional mechanical Davenport operators, when designing the control interface. We made it easy for both groups to run this machine, and lowered the learning curve by simplifying the most common and difficult mechanical adjustments.
Nearly 20 years ago, Davenport established Davenport Machine University to train multi-spindle operators to use and maintain both the Model-B and Servo-B platforms. In the last 10 years, we’ve expanded our program to serve our internal employees as well, training several new classes of green machinists, and providing continuing education for our seasoned craftsmen. We have experience teaching 100’s of graduates, and we can train your workforce too.
Next, check out Part 4 of the Hybrid Blog series, which covers “Machine Upgrades.”