Table of Contents
ToggleThe new Davenport HYBRID is the future of Davenport Multi-Spindle machine tool technology. It incorporates the best of the mechanical versatility you would come to expect from Davenport, and adds to it the CNC Technology you need to address today’s most difficult manufacturing challenges.
In this post, we dive into some of the design enhancements applied to the Davenport HYBRID machine with the goal of increasing profitability and productivity for our customers.
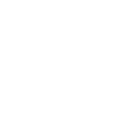
Hybrid Design Machine Features Infographic
Bearings
The first major HYBRID upgrade is how we support the revolving head, or the spindle carrier, into the main machine casting. Older versions of the Davenport Machine had a revolving head that was piloted in a hand-scrapped bore with a few thousandths of running clearance. For the HYBRID platform, we’ve taken our popular HP head design, and upgraded it with a set of 9” diameter bearings to rigidly and accurately mount it to the bed of the machine. This is a ZERO clearance fit, giving you rigid, accurate, and precise work holding so that the workpiece is introduced to the exact same place, every time the machine indexes.
CNC Slides
We then looked at how to deliver the cutting edge to the workpiece. The most obvious differences on the HYBRID platform are the new CNC slides. Gone are the days of dovetail slides, tapered gibs, and the constant adjustments and quality issues that go along with them. Our new CNC slides are modular in nature, so customers are not limited to using old Davenport tooling. They are built upon rigid, pre-loaded linear rail technology, like you would expect to find on high-end CNC lathes and mills. This allows our customers to purchase a brand new HYBRID machine at or near the cost of rebuilding an older Acme, New Britain, or other multi-spindle machine platforms, by moving the same tools into the new HYBRID.
Access Now: Davenport Hybrid Machine – Frequently Asked Questions
2-axis CNC slide
The 2-axis CNC slide on the fourth position will accept standard Davenport tooling, as well as 5/8 square shank stick tooling commonly found on CNC lathes. It gives customers the ability to:
- Do profiling, angular trepan grooves, single point threading etc., with the XZ CNC slide.
- Place ID tooling in this slide, and do INTERNAL grooves, deburring and complex operations from this traditionally external tooling position.
- GANG tools, doing both OD and ID work on the same CNC controlled slide.
- Stagger tools, having a standard end-working tool, like a drill, do it’s work early in a cycle, and once it has backed out, bringing another tool into the bore to machine o-ring grooves on the inside of a part. This way, even though you have a 5 spindle machine, you can bring up to 8 different ID tools into the workpiece.
The XZ slide is standard equipment for the 4th position on the HYBRID, and will be available as an optional 3rd position attachment in the near future.
Davenport DTS Dovetail Tooling System
Toolholders
The new tool holders of the Davenport Dovetail Tooling System (DTS) are available as Skive, Forming or generic 5/8 lathe stick tool configurations. With precision taper adjustments, length positioning, and center height adjustments, the DTS system is the most user friendly tooling to date. And all tool holders are equipped with thru-tool High Pressure coolant porting, which directs a high-pressure knife-edge stream right at the cutting edge of the insert, without placing copper lines and moveable nozzles in the cutting zone.
Inserts
The Davenport DTS is specifically designed to be used with disposable carbide insert technology. Today’s cutting edge technology from major carbide insert OEMs provide the best tool-edge possible at the cheapest cost per part. The advanced tooling materials, hundreds of available coatings, and easy edge replacement make the HYBRID tool changes less frequent, easier than re-grinding, and more efficient.
Next, check out Part 3 of the Hybrid Blog series, which covers “Digital Size Control.”